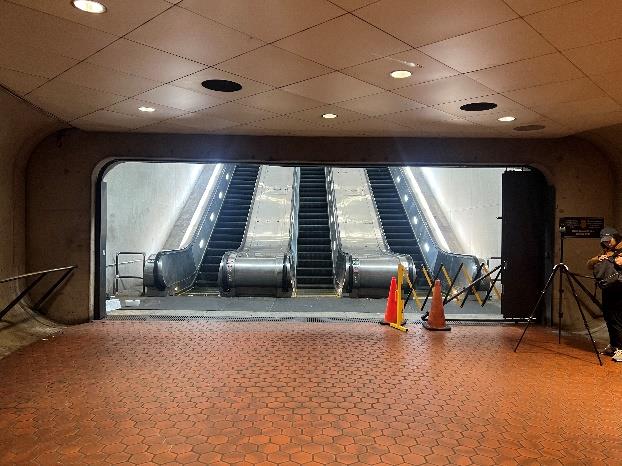
41 Gate Design Replacements at 24 Stations
Overview
CSIE provided Design Services in support of WMATA’s GAEC Facilities Contract. As part of this contract, CSIE provided Project Management Services and Electrical Engineering along with Architectural Design and Structural Engineering, utilizing a sub-consultant for this Task Order.
This Task Order was initially issued to address the need to replace 24 entrance gates at 15 Metro stations due to issues with opening and closing of the gates. The existing gate types included manual and powered overhead coiling grill gates, swing gates, and scissor gates. The project consisted of replacing the gates in-kind where practical, or with an alternative gate type depending on site conditions.
Early in the design phase, the project scope was expanded to the replacement of 41 entrance gates at 24 Metro Stations. Site surveys were conducted at all 24 stations, and documented via Matterport, a Lidar 3D scanning system.
Project Highlights:
Location: 41 Gates throughout the Metro System
Size: Varied by location
Key Project Elements
- Produced a written technical memorandum for each of the six separate bid packages that were designated. The memorandum confirmed issues at individual gate locations that needed to be addressed during the Design Phase.
- CSIE provided deliverables at the 30%, 90%, and 100% construction document submissions.
- Each submission included drawings, specifications, structural calculations, and an estimate of probable construction cost.
- Comment review meetings were also conducted regularly.